The ubiquitous presence of electrical wiring is a cornerstone of modern civilization. Within this intricate network, pvc wire plays a dominant role, prized for their affordability, flexibility, and insulating properties. However, the safe and reliable operation of these essential components hinges entirely on adherence to rigorous safety standards. These standards are not mere suggestions; they are the meticulously crafted blueprints that prevent electrical hazards, ensure longevity, and protect both property and lives. For manufacturers like Anping Shengsen Wire Mesh Products Co., Ltd., a professional entity integrating R&D, production, and sales with dedicated departments for quality and service, embedding these standards into every meter of pvc cable wire is paramount. This article delves deep into the world of pvc wire safety standards, exploring their scope, global frameworks, installation imperatives, material science, and addressing common concerns.
Understanding the Scope of Pvc Wire Safety
Safety standards for pvc wire,encompass a comprehensive range of requirements designed to mitigate risks throughout the product's lifecycle – from manufacturing and installation to operation and eventual disposal. At their core, these standards address:
- Electrical Insulation:The primary function of the PVC jacket is to prevent current leakage and protect users from electric shock. Standards specify minimum insulation thickness, dielectric strength, and insulation resistance values. The inherent insulation properties of quality PVC compounds are fundamental here.
- Fire Safety:Pvc electric wire presents unique challenges in fire scenarios. Standards mandate flame retardancy, low smoke emission, and low toxicity of fumes generated during combustion.Flame-retardant additives are crucial components meeting these requirements.
- Mechanical Protection:Wires and cables must withstand physical stresses encountered during installation and service. Standards define requirements for tensile strength, crush resistance, bend radius limitations, and abrasion resistance. The flexibility and durability offered by a well-formulated PVC coating directly contributes to meeting these mechanical demands. Anping Shengsen's focus on durability ensures their pvc coated wire can endure demanding environments.
- Environmental Resilience:Pvc wire is often exposed to harsh conditions – moisture, chemicals, UV radiation, and extreme temperatures. Standards specify performance criteria for water resistance, chemical resistance, UV stability, and operational temperature ranges. The corrosion resistance provided by a high-quality pvc coating is vital for longevity in moist or chemically aggressive environments, a key feature highlighted by Anping Shengsen.
- Identification and Marking:Clear and permanent markings indicating voltage rating, conductor size, temperature rating, manufacturer identification, and compliance standards are essential for safe installation, maintenance, and inspection.
Global Standards Governing Pvc Cable Wire
The landscape of pvc cable wire safety standards is complex, involving international, regional, and national bodies. Key players include:
- International Electrotechnical Commission: Develops widely adopted international standards . These form the basis for many national standards.
- Underwriters Laboratories: Sets stringent safety standards widely recognized in North America and beyond. UL certification is often a market requirement. Anping Shengsen's commitment to meeting customer inspection standards aligns with achieving such certifications.
- Canadian Standards Association: Publishes Canadian standards, often harmonized with UL standards.
- European Committee for Electrotechnical Standardization: Develops European Norms, often based on IEC standards but with specific regional requirements. The CE marking signifies conformity.
Compliance with these standards involves rigorous testing by accredited laboratories. Manufacturers must demonstrate that their pvc cable wire consistently meets or exceeds the defined criteria for insulation integrity, flame spread, smoke density, toxicity, mechanical strength, and environmental resistance throughout its rated temperature range. Anping Shengsen's dedicated quality inspection department plays a critical role in ensuring this ongoing compliance.
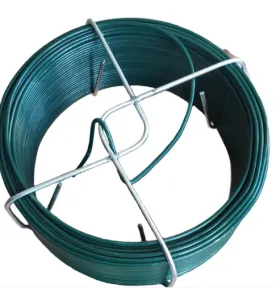
Installation for Pvc Electric Wire
Even the highest-rated pvc electric wire can become a hazard if installed or used incorrectly. Safety standards extend into installation practices and application suitability:
- Voltage Rating:Using wire rated for a lower voltage than the circuit it serves is extremely dangerous. Always select wire with a voltage rating equal to or exceeding the system voltage.
- Current Carrying Capacity:Exceeding the ampacity rating causes overheating, insulation degradation, and fire risk. Ampacity depends on conductor size, insulation type, ambient temperature, and installation method. The temperature tolerance of the PVC compound is a key factor here.
- Environmental Suitability:Pvc electric wire intended for outdoor use must be sunlight-resistant. Wire in wet locations requires moisture resistance. Chemical exposure demands specific chemical resistance. Using general-purpose pvc wire in harsh industrial or outdoor settings without verification invites premature failure. Anping Shengsen's product versatility, including options suitable for outdoor fencing and gates, garden trellises, and potentially specific electrical wiring contexts, relies on formulating PVC for these environments.
- Installation Methods:Standards and electrical codes dictate proper bending radii, securing methods, protection from physical damage , and avoidance of sharp edges. The easy handling and installation characteristic of smooth PVC coating reduces risks during this critical phase.
- Grounding and Bonding:Essential for safety, preventing shock hazards and ensuring protective devices operate correctly. Specific requirements for equipment grounding conductors are mandated.
- Application-Specifictandards:Certain applications have additional rules.Pvc wire in construction reinforcement might need different mechanical specs than wire used in medical devices or data centers, which may demand stringent fire safety (LSZH) and EMI considerations. Understanding the end-use is critical for selecting the correct pvc electric wire.
Material Science in Pvc Wire Production
The safety of pvc wire starts at the molecular level with the formulation of the PVC compound:
- PVC Resin:The base polymer, chosen for its inherent electrical insulating properties.
- Plasticizers:Added to impart flexibility and durability. The type and amount significantly impact low-temperature flexibility, heat resistance, and extraction resistance.
- Stabilizers:Prevent thermal degradation during processing and service, extending the wire's lifespan. Lead-based stabilizers are largely phased out globally due to toxicity, replaced by calcium-zinc or organotin systems.
- Flame Retardants:Essential for meeting fire safety standards. Common types include antimony trioxide, aluminum trihydrate , or magnesium hydroxide. The shift towards LSZH requires non-halogenated flame retardants like ATH or phosphorus-based compounds.
- Fillers:Such as calcium carbonate, used to reduce cost and modify properties, but excessive filler can degrade mechanical and electrical performance.
- Pigments:Provide color options for identification and aesthetics, but must be heat-stable and not compromise electrical properties.
- Special Additives:UV stabilizers for outdoor use, antioxidants for long-term aging resistance, lubricants for processing ease.
Reputable manufacturers like Anping Shengsen, with their dedicated R&D department, invest significantly in formulating compounds that balance cost, processability, performance, and crucially, safety compliance. Stringent control over raw materials and compounding processes ensures batch-to-batch consistency essential for safety-critical applications like electrical wiring.
FAQs acerca de Pvc Wire Safety
What is the maximum operating temperature for standard pvc wire?
Standard pvc electric wire insulation is typically rated for 60°C , 75°C, or 90°C . The specific rating is clearly marked on the cable jacket. Exceeding this temperature continuously degrades the insulation, reducing its lifespan and increasing fire risk.
Is pvc wire safe for outdoor use?
General-purpose pvc wire is not inherently suitable for prolonged outdoor exposure. Sunlight (UV radiation) degrades standard PVC, causing brittleness, cracking, and loss of insulation properties. For outdoor applications, specifically designed pvc cable wire with UV stabilizers added to the compound must be used. Look for markings indicating "Sunlight Resistant," "UV Resistant," or compliance with standards specifying outdoor use.
Does "LSZH" mean pvc cable wire ?
Yes,LSZH stands for Low Smoke Zero Halogen. It refers to pvc cable wire (or other materials) formulated without halogenated flame retardants (like chlorine or bromine) and designed to produce minimal smoke and low toxicity when burned.
How does the thickness of the pvc wire insulation affect safety?
Insulation thickness is a critical safety parameter defined by standards. Thicker insulation provides:
- Higher dielectric strength (withstands higher voltages).
- Better mechanical protection against abrasion, cuts, and impact.
- Improved resistance to environmental factors like moisture ingress.
- Enhanced durability over time.
Using pvc wire with insulation thinner than required for its voltage rating or application is a significant safety hazard, increasing the risk of short circuits, shocks, and fire. Standards precisely specify minimum thicknesses based on conductor size and voltage.
Can pvc wire be recycled, and are there safety concerns?
Recycling pvc electric wire is challenging but possible. The process involves separating the metal conductors from the PVC insulation/jacket. The PVC can then be granulated and potentially reused in non-critical applications. However, safety concerns arise from:
- Hazardous Additives:Older pvc wire may contain lead, cadmium, or certain phthalates, requiring careful handling during recycling.
- Mixed Polymers:Contamination with other plastics reduces recyclate quality.
The safety of electrical systems powered and connected by pvc wire, is non-negotiable. It rests upon a foundation of rigorous international and national standards that govern every aspect, from the molecular composition of the PVC compound to its performance in fire, its mechanical resilience, its environmental endurance, and its correct installation and application. Manufacturers bear a profound responsibility. Companies like Anping Shengsen Wire Mesh Products Co., Ltd., leveraging their integrated R&D, production, and quality control departments, play a vital role by embedding these safety standards into their core processes. They ensure the corrosion resistance, flexibility and durability, insulation properties, and versatility that make PVC coated wire invaluable for applications ranging from fencing and gates and garden trellises to critical electrical wiring and construction reinforcement, is delivered without compromising on the paramount requirement: safety. Choosing compliant products, installed correctly according to code, and understanding the material's limitations are the final, essential steps in harnessing the benefits of PVC wire while safeguarding people and property. The standards exist; vigilance in their application is the key to a secure electrical future.