Choosing the right baling wire gauge is critical for businesses that rely on effective waste management and recycling solutions. Overlooking this aspect can lead to operational inefficiencies and increased costs. With numerous options available in the market, understanding the nuances of baling wire gauges can provide a competitive edge, ensuring operations run smoothly.
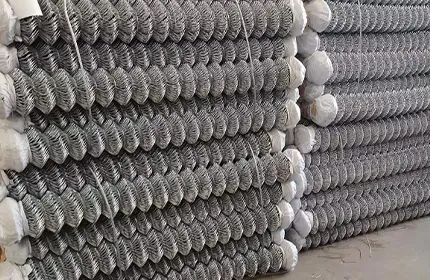
Baling wire is an indispensable tool used to bind recyclable materials, including cardboard, paper, and textiles. The wire’s gauge, or thickness, determines its strength and durability. Gauge numbers follow a reverse logic the lower the number, the thicker and stronger the wire. Selecting the appropriate gauge requires a balance between the materials being baled and the equipment used. A mismatch in these elements could be detrimental, leading to wire breakage or inadequate binding, which could cause operational downtime.
One of the most impressive applications of baling wire can be witnessed in high-volume recycling environments where large, heavy bales are common.
Facilities like these often opt for a thicker wire gauge ranging between 9 to 12. These gauges provide superior tensile strength, ensuring the bales are securely fastened, minimizing the risk of rupture during handling and transport. In contrast, smaller operations that deal with lighter materials might find a 14 or 16 gauge wire to be sufficient. Opting for a thicker gauge than necessary could impose unnecessary costs without any added benefits.
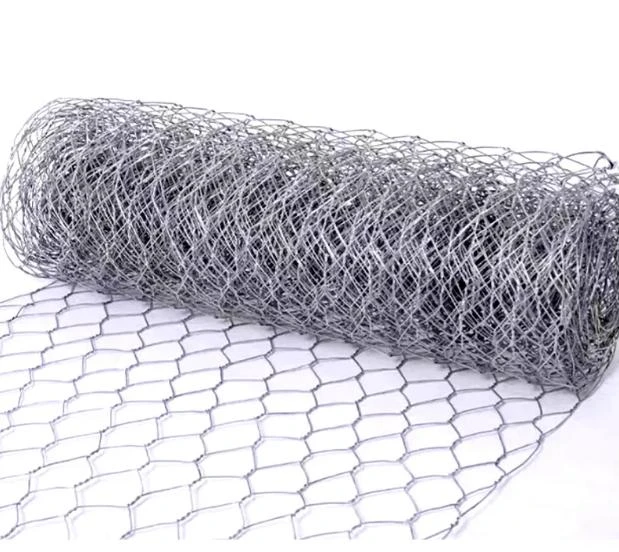
The choice of wire gauge is not merely about strength; it also impacts operational efficiency. A thicker gauge takes more space on storage spools and can affect the speed of the baling process. Operators report that utilizing the exact wire gauge appropriate for their baling machines not only speeds up the process but also extends the lifespan of their equipment, as there is less wear and tear on the machinery components.
An interesting development in the industry is the move towards greener practices. Recyclers are increasingly opting for high-tensile strength wire rather than opting for the thickest gauge. High-tensile wire is made from a specific steel alloy that allows it to be thinner while retaining comparable strength characteristics. This innovation reduces the weight and material usage per bale, driving down costs and environmental impact—a savvy solution for companies striving to meet sustainability goals without compromising on performance.
baling wire gauge
Engaging with experienced suppliers who can offer insights and recommendations based on specific operational needs can significantly enhance the buying decision. Industry veterans suggest inquiring about the wire’s ductility and elongation properties, which affect how the wire behaves when force is applied. Wire that stretches well under duress without breaking can adapt better to varying pressure points, providing an additional layer of security around the bales.
Operational leaders often share their experiences of quality control measures they have put in place. Ensuring each batch of wire meets stringent quality standards before use helps maintain consistent performance. Inspections typically include tests for tensile strength, elongation rate, and corrosion resistance. Suppliers with certifications and compliance with international standards often stand apart in terms of reliability.
The choice of baling wire gauge reflects a company’s commitment to efficiency, cost-effectiveness, and sustainability. As environmental considerations become increasingly important, the recycling industry continuously seeks innovations that allow for these virtues to coexist. The role of the operations team is to stay informed about advancements and assess whether new products can enhance existing systems.
When selecting the right baling wire gauge, consulting resources, and industry experts remains invaluable. This investment in knowledge ensures the right decisions, propelling operations toward increased productivity and sustainability. Companies that leverage this understanding to inform their procurement decisions will likely maintain a competitive advantage, produce less waste, and enjoy long-term cost savings. By making well-informed choices, these businesses not only streamline their operations but also contribute positively to environmental conservation efforts.
In conclusion, the nuanced selection of the proper baling wire gauge is strategic, with wide-ranging impacts on operational efficiency, sustainability efforts, and cost management. By investing time in understanding the specific needs of their facilities, consulting with experts, and prioritizing quality assurance, businesses can ensure they remain at the forefront of the recycling industry.