Selecting the right material for tying applications is a decision that can significantly impact various industries, ranging from construction and agriculture to manufacturing and marine operations. One such material that stands out in this arena is stainless tie wire—a versatile, durable, and reliable solution. This article delves into the specifics, offering a comprehensive understanding of why stainless tie wire is respected across diverse sectors for its performance and dependability.
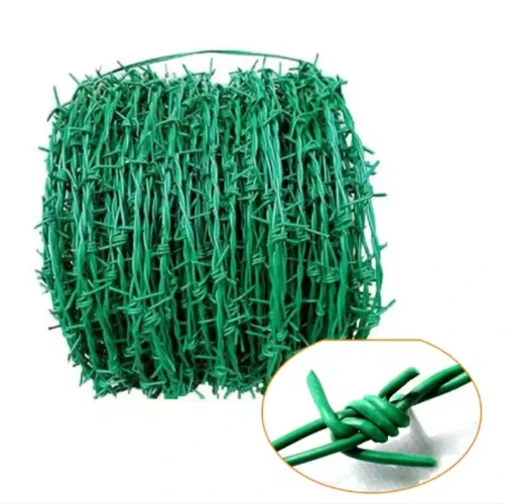
Stainless tie wire is prized for its exceptional resistance to corrosion and rust, making it especially ideal for applications exposed to harsh weather conditions and moisture. Unlike its galvanized counterparts, stainless tie wire maintains its integrity and strength in environments where corrosion can be a significant issue. This makes it a preferred choice in marine environments, wherein exposure to salty air and water can quickly degrade other materials.
An often-overlooked advantage of stainless tie wire is its impressive tensile strength coupled with its flexibility. This dual characteristic ensures that the wire can be both strong and pliable, making it suitable for complex tying jobs that require both a secure hold and adaptability to various shapes. Experts in construction and manufacturing frequently choose stainless tie wire for its ability to withstand high tension without snapping, a result of its robust yet flexible nature. In fact, continuous industry feedback emphasizes its critical role in reinforcing structures, fastening elements in critical alignments, and in situations where both quick application and enduring stability are paramount.
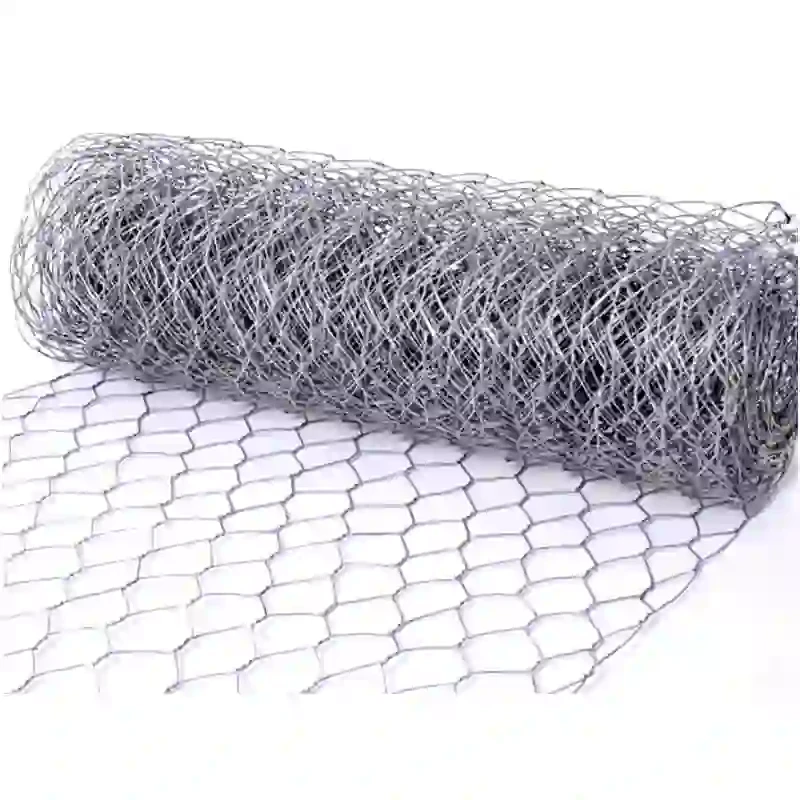
Furthermore, the non-reactive nature of stainless tie wire makes it invaluable in industries like food processing and pharmaceuticals. In environments that demand stringent hygiene and chemical neutrality, stainless steel’s inherent characteristics prevent contamination risks. This specificity in industry use significantly underpins its authority and support from experts who require materials that comply with stringent safety and cleanliness standards.
stainless tie wire
However, the expertise needed to appropriately select and apply stainless tie wire cannot be understated.
Professionals need to understand the gradations and types of stainless steel to optimize their usage. For instance, Type 304 stainless steel offers broad application possibilities, but in environments riddled with extreme corrosive elements, Type 316 may be more suitable due to its enhanced molybdenum content, which increases its resistance to such conditions. This demonstrates the critical need for specialist insights when deploying stainless tie wire in challenging environments, an insight drawn from seasoned metallurgists and engineers who have analyzed and reassessed these materials over years of practical use.
In terms of installation experience, those who regularly work with stainless tie wire note the versatility and long-term cost efficiency it provides. Despite a higher initial cost compared to lesser-grade materials, its durability significantly reduces replacement needs, offering long-term savings especially noteworthy in large-scale projects. The installation process is lauded for its straightforwardness—professionals often highlight how its malleability reduces the strain and effort typically associated with tying and securing tasks, speeding up processes and improving productivity on work sites.
In conclusion, stainless tie wire represents a meeting point between tradition and innovation, maintaining its place of trust within industries due to its unparalleled reliability and versatility. Its performance in various settings supports its reputation as a go-to material, affirmed by professionals who continuously seek optimal, enduring results in their work. For any project where durability, reliability, and safety are the top concerns, stainless tie wire is more than just a material choice—it’s a critical component of quality and excellence.